How to Reduce Solar Project Timelines & Costs with Integrated Switchboards
- Castillo Engineering
- Jul 22, 2024
- 4 min read
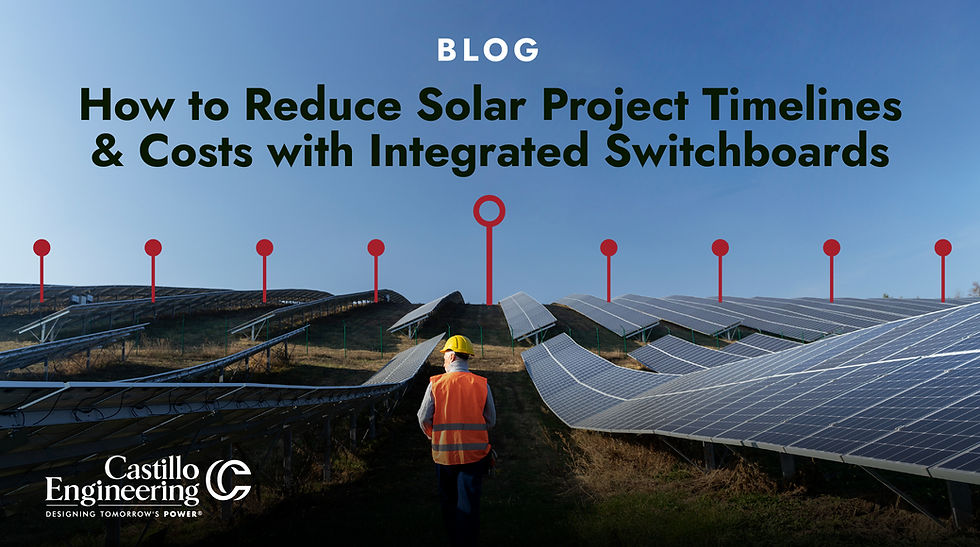
The utility-scale solar energy sector is rapidly evolving, with evolving innovations aimed at reducing costs and increasing efficiency. One such innovation is building fully integrated switchgear skids - which consist of transformers plus switchboards and SCADA - in a factory setting as opposed to integrating these components in the field. By integrating these components in a factory setting, you can streamline installation processes, save tens of thousands of dollars - including through reducing conduit, wire, labor, and time - per project, and deliver the highest quality installations. Below, we cover how Castillo Engineering, Recon Corporation, EPEC & ReBoSS are achieving these benefits today by designing skids and delivering fully integrated transformer (XFMR) / switchboard (SWBD) skids in advance in a factory rather than at solar sites.
Understanding Switchgear in Solar Projects
Switchgear is a crucial component in electrical systems, comprising switches, fuses, and circuit breakers that control, protect, and isolate electrical equipment. In solar projects, switchgear plays a vital role in managing the flow of electricity between solar panels, inverters, and the power grid. By integrating switchgear into the design phase & building them into skids in a factory before arriving on-site, you can significantly reduce costs, expedite project timelines, and improve your solar energy system's overall performance and reliability. Avoiding over-specification in fault current ratings is critical.
Benefits of Integrating Switchgear into Solar Designs
1. Shortest Lead Times
Integrating the XFMR, SWBD, and SCADA in a factory setting is not subject to weather and other supply chain issues that often plague completing this integration in the solar farm field. For this reason, EPEC, ReBoSS and Castillo Engineering can ensure the shortest lead times in the industry for developers and EPCs like Recon Corporation. Also, this reduction in construction time due to lack of weather and labor delays means the developer can cease their construction loans faster, which increases the solar project’s profitability.
2. Highest Quality Installations
ReBoSS and EPEC are highly competent in designing & delivering fully integrated XFMR/SWBD skids custom-designed to power renewable energy projects. Over the years, EPEC has built a specialized team that ensures that the highest quality XFMR/SWBD skids can arrive on time and with superior quality assurance and quality control. Unlike when switchgear, transformer, and other components are integrated on the pads in the field, completing this integration in a controlled environment, factory setting with a highly trained team dramatically increases the quality control and it lessens the time required to complete the switchgear integration.
3. Reduced Installation & Equipment Costs
Integrating switchgear onto skids within a factory setting versus in the field yields significant cost savings. Pre-integrated systems reduce labor costs because labor hours spent in a factory to install switchgear are less than the time spent integrating the same equipment in the field. EPEC, ReBoSS and Castillo Engineering customers have reported saving between $9,000 and $20,000 per transformer/switchboard connection when using a direct bus versus the typical cable connection. With the direct bus and skid connection, there is a significant reduction in cost because there is less conduit, wire, and labor to procure compared to the direct bus connection alternative. Close-coupling the XFMR & SWBD and integrating it on a skid significantly reduces the scope of work and time required for the highly specialized medium voltage labor to complete this switchgear integration in the field. This avoids unnecessary, extremely labor-intensive elements that would otherwise elongate schedules from weather delays, including excavation, pad forming, conduit installation, equipment setting, cable pulling, an excessive amount of high ampacity cable terminations, and equipment grounding conductor runs.
4. Maximum Tax Savings
The new Inflation Reduction Act (IRA) law allows for “manufactured” equipment with domestic content to be counted as part of the percentage required to qualify for certain incentives. Equipment that is built on a solar site is not considered a “manufactured solution” equipment and therefore cannot be counted in the percentage. Integrating the switchgear onto a skid in a factory setting fits this definition. As a result, solar developers can leverage IRA tax incentives to maximize the project’s financial returns.
5. Simplified Maintenance
A well-integrated switchgear system simplifies maintenance and troubleshooting. A comprehensive design that includes switchgear from the outset makes it easier to identify and address issues, reducing downtime and maintenance costs. This ensures that the solar system operates smoothly with minimal interruptions. An above-grade bus is going to have fewer issues than below-grade circuits over the life of the farm. Even if there is an issue down the road, it is much simpler to troubleshoot/repair.
6. Scalability
Integrated switchgear designs are often more modular, allowing for easier expansion and scalability. As your energy needs grow or as you decide to increase your solar capacity, an integrated system can be more readily adapted and expanded without extensive redesign or additional components.
Optimizing solar projects with factory-integrated switchgear skid designs offers a range of benefits, from reduced lead times and costs to simplified maintenance and scalability. Castillo Engineering has already demonstrated proof of concept for this innovative strategy in a portfolio of 10 community solar projects in Illinois with Recon Corporation. The company also has 80 transformer/switchboard integration packages in its pipeline.
Get in touch with Castillo Engineering to learn how to embrace this new approach to maximize the performance and return on investment of your large-scale solar projects.
Kommentare